As part of Industry 4.0 and the smart factory, intelligent systems independently control their own production process. The aim is to maximize operational efficiency through the most comprehensive automation possible. Fluid management should also be taken into account in automation projects in order to avoid deviations and the associated production downtimes. And this is precisely where the experts from Zeller+Gmelin and HYDAC come in: With the help of the newly developed fluid management system "ZG Fluid-Check Pro", the cooling lubricant supply of machines and systems can be automatically monitored, organized and controlled. It incorporates Zeller+Gmelin's many years of expertise in fluid management. One of the first practical users of the newly developed system is Heron CNC-Technik from Vorarlberg in Austria.
The smart device monitors the fill level and measures the concentration, pH value, conductivity and temperature in real time - the current measured values are displayed on the dashboard every minute. In addition, up to four further values such as nitrite or, for example, the proportion of tramp oil can be entered manually. In the event of deviations from the target concentration, readjustments are made automatically. Cooling lubricant profiles can also be stored, whereby the top ten most common water-miscible cooling lubricants from Zeller+Gmelin are already stored, so that the user only has to select their preferred product on the display without having to enter any additional parameters. Two dosing pumps can be connected for the automatic addition of actuating agents/inhibitors. Together with a multiplexer, one system monitors up to seven CNC machines. "Our fluid management system permanently records the emulsion status so that traceability is also guaranteed," emphasizes Thorsten Wechmann, Strategic Business Unit Manager at Eislingen-based lubricant manufacturer Zeller+Gmelin.
As an independent company within the family-run Heron Innovations Factory, Heron CNC-Technik GmbH specializes entirely in metal and plastic processing. As a contract manufacturer for milling and turning, Heron uses state-of-the-art CNC machining centers to produce prototypes and series parts in batch sizes of 1 to 10,000. Customers come from a wide range of industries such as medical technology, special machine construction, automotive and semiconductor technology. "We want to meet the demands of increasing competition and a growing customer base, which is why we rely on end-to-end, automated processes in the spirit of Industry 4.0," sums up Manuel Gmeiner, Managing Director there. "Most of our machines run fully automatically, around the clock, 365 days a year."
Manufacturing processes and techniques are constantly being developed further. However, one hurdle to 'unmanned' production is cooling lubricant management. Fill levels have to be checked regularly and refilled manually - even on public holidays or at weekends. "A lubrication failure could not only bring the machine to a complete standstill, but also cause damage," says Heron Managing Director Manuel Gmeiner.
Digital factory: maintenance is often forgotten
And Thorsten Wechmann from Zeller+Gmelin poses the question in the direction of the smart factory: "What use is the simulation of production and the elimination of interference contours in the machining process if an employee has to intervene at the machine at the end because the fill level or other parameters of the cooling lubricant are not correct? Self-organizing production always includes the ability to take timely and automated countermeasures if there are deviations from defined values. A deviation in the cooling lubricant must not become a bottleneck." Although solutions already exist today that allow current lubricant values or key figures to be transmitted to a smartphone via SMS, "if there is a deviation, someone still has to make manual adjustments," continues Thorsten Wechmann.
Smart monitoring for SMEs
"In order to ensure long-term competitiveness as a medium-sized company, there is often no way around a high degree of automation and the associated digitalization of processes," emphasizes Philipp Götz, Product Manager at HYDAC Filter Systems GmbH: "Our goal is to support manufacturing companies on their way to Industry 4.0. With the ZG Fuid-Check, we have developed a compact device that can not only monitor the entire cooling lubricant cycle of up to seven machines and central systems simultaneously, but can also intervene independently and regulate in the event of deviations."
Fluid management from Eislingen
In Zeller+Gmelin, the company has also found a suitable cooperation partner. As a long-standing supplier of water-miscible cooling lubricants, which are available from Zeller+Gmelin under the brand name Zubora for machining production. With ZG Fluidmanagement GmbH, a separate subsidiary was even founded for this purpose. "Many modern companies now rely on effective fluid management, which is essentially based on the analysis and conditioning of liquid working media as well as precise consumption recording and evaluation. The aim is to increase efficiency by, among other things, maintaining the target concentration and preventing under-concentration.
This also results in longer tool life and better surface qualities in the machining process," Thorsten Wechmann knows from numerous practical applications. However, too high a concentration also has negative effects: On the one hand, more lubricant is consumed, on the other hand, the foaming behavior of a cooling lubricant can change. If all parameters are always optimally adjusted, the lubricant can be used for much longer and with process reliability.
"Of course, we are also constantly dealing with the question of how lubricant management can be further optimized." When it comes to fluid management systems, there is still a lot of room for improvement on the market. Many devices are not capable of flushing. This makes them inaccurate and requires constant readjustment - not so the ZG Fluid-Check. The device is also very compact and fits into any production area. "The very first projects were successful and we were able to benefit from each other's experience and pass it on to the user. Our customers can now purchase the system from our Fluid Management division, naturally in combination with our own Zubora high-performance cooling lubricants, which are gentle on the skin and resources."
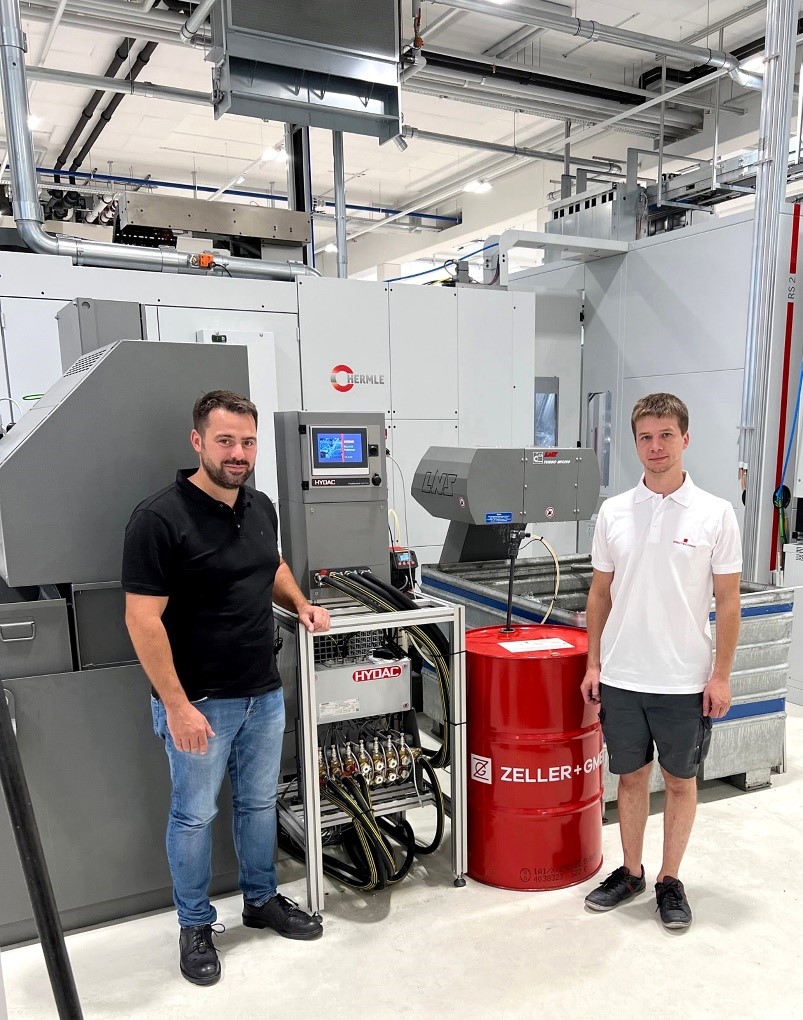
And Phillip Götz from HYDAC adds: "Medium-sized industrial customers in particular want an 'all-round carefree package' from their lubricant suppliers so that they have time internally for their core business. By selling our devices, Zeller+Gmelin is also specifically targeting companies that want highly automated production but do not want to provide additional resources for fluid management. The machine operator then no longer has to measure, refill and readjust at the machine. This is an enormous time saving and therefore more time for value-adding tasks."
High-precision prototypes and series parts in machining technology
Manuel Gmeiner from Heron agrees: "The collaboration with Zeller+Gmelin and HYDAC is another important building block for us towards the complete digitalization of our production." The ZG Fluid-Check is currently being tested on a fully automated Hermle system in which a robot system equips three 5-axis milling centers. The system is connected to an autonomous transport robot system from Servus Intralogistics, another Heron Innovations Factory company. "This allows the system to be operated fully automatically 24/7." Following a successful trial phase together with Zeller+Gmelin, Heron opted for two of the devices with multiplexers, to which up to 14 machines can be connected and supplied.
Digital, intuitive and user-friendly
In addition to the fill level, the device continuously measures the concentration as well as the pH value and other parameters. In order to keep the concentration at the desired level, the dosing pump counteracts this in good time if necessary. This also prevents all risks that could be associated with under/over-concentration, such as foaming or impairment of corrosion protection. "The values can either be read directly on the touch panel of the device or from outside - for example on a PC or tablet. A user-friendly dashboard clearly summarizes all the information so that it can be presented in a maintenance meeting, for example, or is permanently available to the staff, even without them being directly in front of the system," explains Phillip Götz.
Multiplexer for up to seven machines simultaneously
Two devices are currently in use at Heron. The solution is to be extended to eleven more machining centers at a later date. Manuel Gmeiner's experts also want to test the multiplexer , which can monitor up to seven machines simultaneously.
"The multiplexer ensures continuous monitoring and readjustment of the cooling lubricant concentration and is particularly suitable when several individually filled, robot-controlled systems are in use, as is the case with Heron," explains Philipp Götz. And Markus Müller from ZG Fluidmanagement adds: "Our employees are specially trained for such installations so that we can offer the most comprehensive support and service possible." "The system is extremely smart and will quickly pay for itself," concludes Manuel Gmeiner, Managing Director of Heron. "Lubricant is now not only automatically refilled in the correct concentration, but also provides additional measured values. This allows us to permanently monitor the concentration of our lubricant, which has significantly improved reliability. We also no longer have to carry out continuous manual checks, so our colleagues can concentrate on their actual work."
Now that the ZG-Fluid-Check Pro has proven itself in practice right from the start, an extension for multi-machine supply is already planned for 2023: the ZG-Fluid-Check Neo can connect several machines at once via a ring line and ensure efficient fluid management.
Advantages of the "ZG Fluid Check Pro" coolant condition monitoring system at a glance:
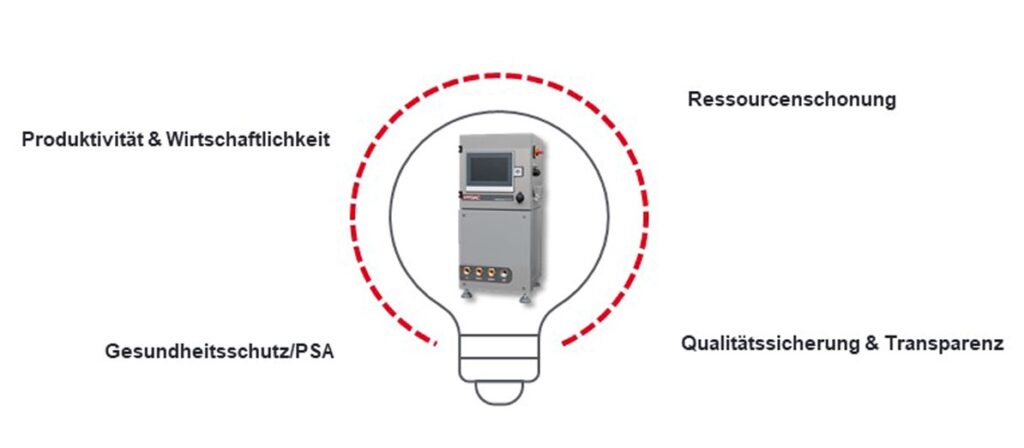